APSX-PIM Automatic Plastic Injection Molding Machine
Since 2017, we have improved the APSX-PIM that makes plastic injection molding affordable and easy. Today, the APSX-PIM is an alternative to the traditionally expensive, overpowered and large injection molding machines used for production, R&D, prototyping, product design, education, research and other plastic part production environments. It is a perfect recipe for sustainable manufacturing.
The PIM machine is capable of ejecting molded parts based on the type of mold you use. If you use a mold with ejector pins it will continuously eject (Multi-mode). If you use a mold without ejector pins (like the test mold that comes with it) you will eject the part manually at the end of each cycle (60 secs). (single-mode).
Compact Size - APSX Machines feature a space-saving and streamlined design, perfect for desktop or limited workspaces. A real injection machine without the typical compromises of desktop injection presses. The APSX-PIM is an automated injection molding machine and has the ability to make parts much more than a rough draft prototype plastic part. It can be moved into nearly any workbench and requires only basic 115VAC (US) or 230VAC (EU) wall outlet to operate. Standard mold size is 6" by 4.8" as it is stated for the Blank Mold available here. The mold installation process can be done in 15 minutes.
Optimized Risk Control: APSX Machines are engineered for simplicity in mind to maximize efficiency with minimal learning curve to save time and initial investment costs. APSX-PIM machines are user-friendly and intuitive, allowing your team to quickly adapt and operate them with ease. By minimizing the risk associated with complex machinery, APSX Machines empower your workforce to explore new product possibilities with no fear.
Minimal Waste: APSX Machines facilitate eco-friendly production, promoting lean manufacturing and minimizing waste generation. We understand the importance of sustainability in today's world, and our machines are built to reduce material waste during the production process.
Precision and Accuracy: APSX Machines ensure consistent industrial-quality outputs, delivering precise and accurate production results. Smaller doesn't mean less capable. The repeatability is an important process parameter that most of the benchtop injectors can not offer. The APSX-PIM uses the latest available technology for precision and repeatability. The user screen offers multiple controls and is a user friendly one.
Adaptability to Changing Requirements: APSX Machines seamlessly adapt to flexible and responsive production needs with quick setup times. As a business, you understand the importance of being agile and responsive to market demands. APSX Machines offer the flexibility you need to switch between different production requirements with ease.
Cost-Effective Performance: APSX Machines offer cost-effective performance by minimizing both initial and ongoing operational costs. Their small batch capabilities enable optimal production efficiency while maintaining cost control.
Time to Market Faster: APSX Machines enable rapid manufacturing with a short learning curve and simple setup procedures, ensuring agility and fast time-to-market. In today's competitive landscape, being the first to market can make all the difference. APSX Machines empower you to accelerate your production process, reduce lead times, and gain a competitive edge.
This plastic injection molder creates quality parts that are consistent, easily repeatable and affordably produced. You can create low-cost components rapidly without complex setup or large up-front costs. The complex plastic part features such as molding internal threads, micro molding, overmolding and thin wall molding can be made without high cost molds. The aluminum tooling is perfectly fine for niche applications such as medical device or other medical applications for the medical industry or other similar industries. The APSX-PIM can replace the cnc machining parts by using tough plastics such as Delrin and Polycarbonate for a better surface finish and much shorter cycle times.
APSX-PIM can process any plastic including but not limited to Polypropylene (PP), glass filled Polypropylene (PP), FDA approved plastics, Polyethylene (PE), Thermoplastic Polyolefin (TPO), Nylon, Polycarbonate (PC), Acetal (Delrin), ABS, PC/ABS with MFR (ASTM D1238) > 3 g/10min).
Here are some PLASTIC MATERIAL SELECTION TIPS.
APSX-PIM Applications: Who needs a small injection molding machine?
It is so easy to unbox and setup. You can make your first part in 30 minutes once you receive the APSX-PIM.
KEY FEATURES OF APSX-PIM
- Compact design (4 ft by 1 ft footprint)
- Strong body structure with stainless steel, hard anodized aluminum, and bronze parts
- Wear resistant bronze barrel and case hardened steel plunger with hard chrome plating made in Ohio
- All electric and no water-coolant system
- Full automatic (MULTI MODE) with precision sensors
- Auto Heat Off after 5 minutes inactivity
- Injection speed control for fill rate
- Electronic temperature control system
- Multi heat zone control
- User touch screen for operational control
- Typically 60 secs per injection cycle (clamp opens and ejects parts every 60 secs)
USER MANUAL (PDF)
BROCHURE (PDF)
SAMPLE PARTS MADE BY APSX-PIM: Do you want to see some sample parts? Click here
What's in the crate?
APSX-PIM
Demo mold
Mold insulator
Demo test parts made by APSX-PIM sold
Polypropylene plastic pellets for you to get started making parts
Tablet PC with APSX-PIM software installed
All components of this machine are made in Cincinnati, OH USA. CE compliant. 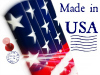
Showroom meeting is available with appointment. Please SCHEDULE a call or showroom demo day.
.:. Dream. Design. Make NOW. .:.
Watch APSX
YouTube
|
- |
Schedule
a Visit or Call
|
- |
APSX-PIM
User Guides
|
 |
- |
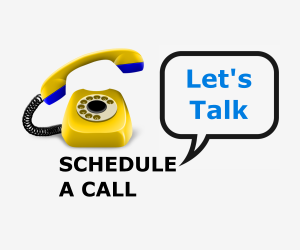 |
- |
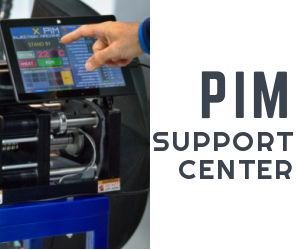 |
DO YOU NEED FINANCING?
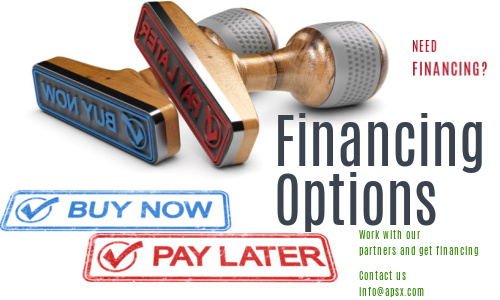
moirons, minijector, formlabs, arburg, all3dp, fictiv, micro-molder, abplasticinjectors, babyplast, boymachines, mediummachinery, techkits